In Tanzania’s booming mining industry, effective conveyor system maintenance is a critical factor in ensuring productivity and operational efficiency. Mining companies rely on these systems to transport ore, minerals, and waste materials efficiently across expansive mining sites. However, harsh conditions such as dust, moisture, and abrasive materials can quickly degrade this vital equipment if regular maintenance is neglected. By prioritizing routine maintenance, companies can minimize downtime, extend equipment lifespan, and reduce long-term costs.
Why Conveyor System Maintenance Is Essential
Conveyor systems are the backbone of material handling in mining operations across Tanzania. Maintaining these systems is non-negotiable because high-quality maintenance practices offer significant benefits, such as:
- Reducing Mining Downtime: Scheduled upkeep prevents unexpected breakdowns that could halt production.
- Enhancing Operational Efficiency: Well-maintained systems operate at optimal speeds and ensure a steady flow of materials.
- Extending Equipment Lifespan: Routine inspections and repairs protect against wear and tear, lowering the need for frequent replacements.
Key Components of Effective Conveyor System Maintenance
Successful maintenance of conveyor systems involves a combination of proactive inspections, timely repairs, and the use of quality components. The process begins with regular inspections and cleaning. Visual checks help identify early signs of wear, misalignment, or damage on components such as conveyor belts, rollers, and pulleys. Keeping the system clean is crucial because accumulated dust and debris can accelerate wear and cause component failure.
Preventative maintenance is equally important. This includes scheduled servicing and timely replacement of worn parts like rollers, bearings, and belts to prevent unexpected system failures. Advanced diagnostic tools, such as vibration analysis and thermal imaging, are invaluable for early detection of potential issues. These technologies enable mining companies in Tanzania to make data-driven decisions and plan maintenance activities effectively, ensuring continuous operation even under harsh conditions.
Benefits of Regular Maintenance in Tanzania’s Mining Sector
Implementing a robust conveyor maintenance program offers significant benefits for Tanzania’s mining industry. Consistent upkeep minimizes downtime by ensuring that conveyor systems run smoothly, reducing both the frequency and duration of unexpected stoppages. Regular maintenance enhances safety by reducing the risk of equipment failures that can endanger workers in hazardous mining environments. In addition, well-maintained equipment guarantees a steady material flow, boosting overall productivity. Finally, preventative maintenance reduces the need for costly emergency repairs and extends the operational life of critical mining equipment, resulting in substantial cost savings.
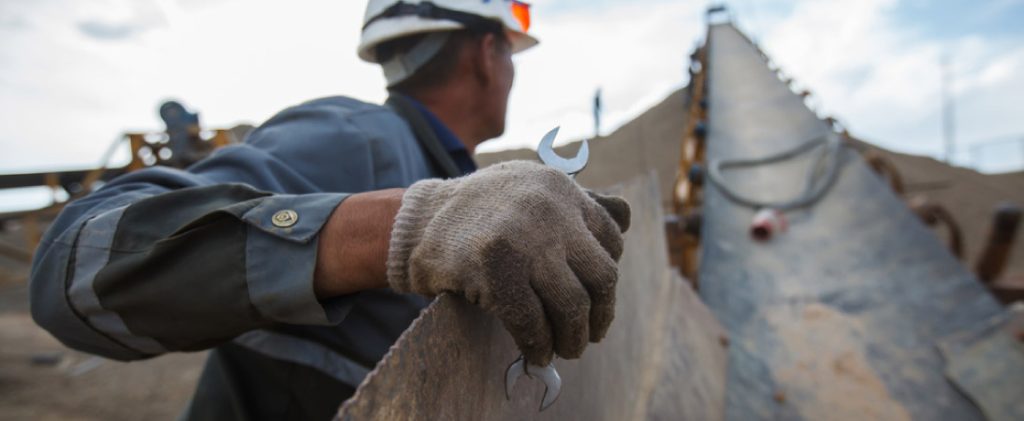
Challenges and Solutions for Conveyor Maintenance in Mining Operations
Tanzanian mining companies face several challenges when it comes to maintaining conveyor systems. Harsh environmental conditions—extreme temperatures, abrasive materials, and high humidity—can accelerate wear on mining equipment. To address these challenges, companies should invest in durable, high-performance components and schedule regular inspections to catch issues early. Unplanned downtime caused by unexpected breakdowns can significantly disrupt production, so implementing a proactive maintenance schedule with real-time monitoring technologies is essential to predict and prevent failures. Additionally, limited technical expertise or equipment can hinder effective maintenance, which can be overcome by collaborating with experienced service providers specializing in mining equipment maintenance.
Proactive Strategies for Minimizing Mining Downtime
To maximize efficiency and further reduce downtime, Tanzanian mining companies should adopt proactive strategies, such as:
- Developing a Detailed Maintenance Schedule: Cover all critical components of the conveyor system.
- Investing in High-Quality Spare Parts: Use advanced materials designed to withstand the rigors of mining operations.
- Training Technical Staff: Ensure that your team is well-versed in the latest maintenance techniques and technologies.
Utilizing Data-Driven Technologies: Employ analytics and IoT devices to monitor equipment performance for timely interventions and smarter maintenance planning.
Conclusion
Efficient conveyor system maintenance is more than just a routine task; it is a strategic investment in Tanzania’s mining industry. By prioritizing regular inspections, preventative care, and the integration of advanced diagnostic tools, mining operations can significantly reduce downtime, lower maintenance costs, and boost productivity. For mining companies looking to maintain a competitive edge in a demanding environment, implementing a robust maintenance program is essential for long-term success. Adopting quality maintenance practices today will pave the way for higher efficiency, improved safety, and sustained economic growth in Tanzania’s dynamic mining sector.
To achieve these maintenance goals, partnering with an experienced and reliable service provider is crucial. Reed Engineering, based in Tanzania, specializes in delivering comprehensive supply solutions and advanced engineering expertise to the Mining, Oil & Gas, and Industrial sectors. Our commitment to quality and sustainability ensures that your conveyor systems operate at peak performance, minimizing downtime and extending the lifespan of your equipment.